[제35주차 IR52 장영실상] 현대차 / 일체형 핫스탬핑 사이드 아우터 레인프
등록일2019-08-29
왼쪽부터 허준무 센터장, 이해훈 연구원, 위성개 파트장, 오세훈 팀장.
현대자동차가 개발한 `일체형 핫스탬핑 사이드 아우터 레인프`가 2019년 35주 차 IR52 장영실상을 수상했다.
자동차를 구성하는 주요 뼈대를 `차체(BIW·BODY IN WHITE)`라고 하는데, 아우터 레인프는 차체 측면, 즉 차량 앞문 부위를 말한다. 현대차가 개발한 일체형 핫스탬핑 사이드 아우터 레인프는 900도 이상 가열된 철강 소재를 프레스에 넣어 원하는 형상으로 만든 뒤 급랭시켜 가볍고 강한 부품을 만드는 기술인 핫스탬핑 공법을 적용한 초고강도 강판을 차량 문에 적용한 기술이다. 정면이나 측면 충돌 또는 차량 전복 시 차체 변형을 억제해 외부 충격을 줄여 승객을 안전하게 보호하는 공간을 확보했다는 평가를 받고 있다.
현대차는 여러 부품을 나눠 핫스탬핑을 해오던 관행에서 벗어나 일체형 구조에 집중했다. 이해훈 현대차 차체설계2팀 연구원은 "핫스탬핑 공정을 줄이면 생산성이 증가할 뿐 아니라 용접 부위가 줄면서 더 우수한 안전성 확보도 가능하다"며 "일본 기술을 극복하기 위해 현대자동차는 두 개 강판을 나누어 붙이는 공법 대신 1.1㎜짜리 얇은 강판 하나로 자동차 문을 만든 뒤 곧바로 핫스탬핑을 적용하자는 계획을 세우고 연구개발(R&D)을 시작했다"고 말했다. 그런데 1.1㎜짜리 얇은 강판을 핫스탬핑할 때 변형이 발생하는 문제가 있었다.
결국 현대차 연구진은 설계 디자인을 수차례 바꿔가면서 실험을 반복, 세계 최초로 1.1㎜의 얇은 일체형 핫스탬핑 사이드 아우터 레인프를 개발하는 데 성공했다. 일체형으로 만들면서 최적화 설계를 통해 12개 부품을 없애 무게를 2㎏가량 줄이는 데 성공했다. 일체형으로 여러 부품을 결합하는 과정을 없애면서 시간당 제품 생산량도 높아졌고 품질도 향상됐다. 이 연구원은 "일체형 구조는 부품 간 이음새가 없다는 장점이 있어 외부에서 힘을 받았을 때 하중을 균등하게 분산시킬 수 있다"며 "중량을 절감하면서도 세계 최고 수준의 충돌 성능을 확보했다"고 강조했다.
현대자동차
일체형 핫스템핑 사이드 아우터 레인프
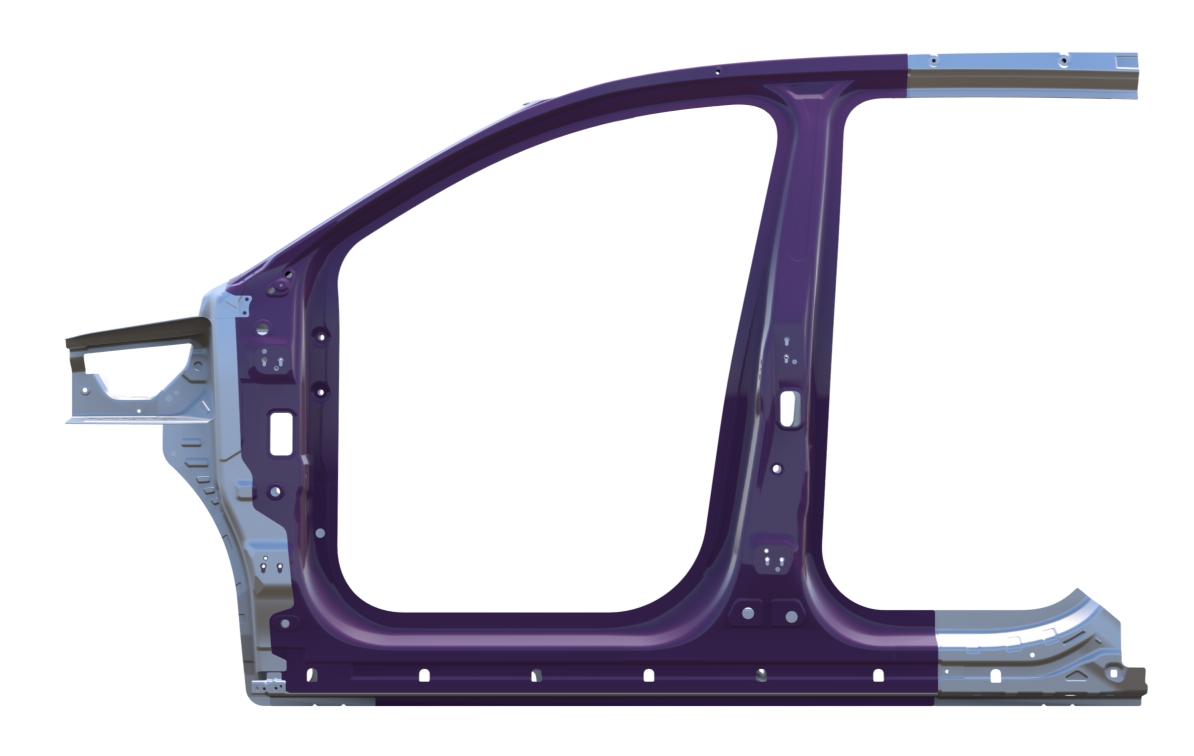
- 용도 및 기능
- 일체형 핫스템핑 사이드 아우터 레인프는 차체 BIW(BODY IN WHITE)의 측면을 구성하는 부품으로, 초고강도 (핫스템핑) 강판 적용을 통한 정면, 측면 충돌 및 차량 전복 시 차체 변형을 억제하여, 외부 충격에 대한 승객의 안전보호 공간을 확보하고, 일체형 구조의 강성 증대를 통한 안정감 있는 주행성능을 제공하는 기능을 합니다. 세계 최초로 1.1mm (박판)두께의 일체형 핫스템핑 구조를 싼타페(TM) 에 양산적용하여 경량화 및 세계 최고수준의 충돌 안전성을 확보하였습니다.
- 차별적 특징
- <멀티피스의 단점> 일반적인 차량의 경우, 충돌 강건성을 확보하기 위해 사이드 아우터 레인프의 각 주요 부재에 핫스템핑을 적용 한 후, 부품 간 상호 용접하는 멀티피스 구조를 채택 해 왔습니다. 멀티피스 구조는 핫스템핑-핫스템핑 부품 간 용접이 불완전하게 되는 용접 강도 문제, 충돌 시 부품간 접합부에서 발생하는 파단 문제점이 있습니다. 이러한 문제점을 보완하기 위해서 부품 간 접합부의 오버랩구간을 증대하거나, 접합부의 파단 예상 부위에 추가적인 보강재를 적용하게 되는데, 이는 중량 및 부품수가 증가되어 차체의 원가 상승 및 연비 경쟁력이 낮아지는 단점을 가집니다.
따라서 멀티피스 구조의 단점을 근본적으로 해결 하기 위해서 사이드 아우터 레인프를 구성하는 부품(A필러,B필러,사이드실 등)을 핫스템핑 공법으로 한번에 통합하여 성형하는 기술이 개발되기 시작하였는데, 일본의 혼다에서 2개의 강판을 레이져로 용접하여 붙인 후 핫스템핑 공법으로 일체성형 하는 TWB일체형 핫스템핑 사이드 레인프 구조를 개발하였습니다. 하지만 TWB 공법의 경우, 개별의 강판을 철강사로 부터 공급 받은 후, 두 강판을 레이져 용접을 하는 별도의 공장으로 이송하고, 다시 강판을 성형을 하는 공장으로 이송을 해야 하므로, 물류 비용이 증대 되고, 제품을 생산하는 시간이 길어지므로 원가 경쟁력과 생산성이 현저히 낮습니다. 또한, 일체형 사이드 아우터 레인프 부품에서의 TWB의 공법은 독일의 벤틀러사에서 2004년에 특허 출원하여 권리 유지중인 사항으로, 일체형 부품에서 강도나, 두께가 상이할 경우, 특허 침해가 되며, 미국의 GM에서 2011년에 출원한 TWB 핫스템핑 제작방법에 관한 특허에 저촉 될 우려가 매우 높습니다. 따라서, 타사의 특허 침해를 문제 삼아 , 판매 중단이나, 판매 대수에 따른 별도의 로얄티 지급이 될 가능성이 있습니다.< 일체형 구조의 장점> 당사에서는 일반적인 멀티피스의 단점과, 일본에서 적용한 TWB공법의 단점을 모두 개선함과 동시에, 타사의 특허를 침해하지 않고, 세계최초로 박판의 1.1t의 일체형 핫스템핑 사이드 아우터 레인프를 개발하여, 싼타페 TM에 적용하였습니다. 또한 차체 경량화를 위해 박판의 1.1t를 적용할 때, 성능을 극대화 시킬 수 있는 차체 핵심 설계 구조 특허를 출원 및 등록 하였습니다. 이는 차체 설계 기술을 선점하여 경쟁사의 진입 장벽을 높여서, 당사의 경쟁력을 유지 하기 위함입니다. 결과적으로, 당사의 기술은 선행차종인 쏘렌토UM대비하여, 부품수 12개, 중량 2kg를 절감하면서도, 차체 전 영역의 성능을 개선하여, 정면, 측면, 전복 강도를 복합적으로 평가하는 북미 NHTSA와 유럽 NCAP에서 5스타를 받았으며, 북미 IIHS에서 TSP+(top safety pick +) 등급의 세계최고 수준의 안전성을 입증받았습니다.
- 담당부서
- 연구개발본부 바디기술센터 차체설계실(0313680028)
'판교핫뉴스1' 카테고리의 다른 글
응급의료전용 ‘닥터헬기’ 이륙 …대한민국 항공의료에 새 지평 마련-경기도, 29일 도청 내 잔디광장에서 ‘응급의료전용헬기 종합시뮬레이션 훈련’ (0) | 2019.08.30 |
---|---|
도미니카공화국 화장품 바이어에게 듣는다[KOTRA & KOTRA 해외시장뉴스] 및 기타 해외시장동향 (0) | 2019.08.29 |
국민중심·경제강국, 2020년 예산안 및 2019~2023년 국가재정운용계획 (0) | 2019.08.29 |
제3차 지능형 로봇 기본계획 공고 (0) | 2019.08.29 |
「핵심뿌리기술」 지정요건 등 구체화-‘핵심뿌리기술’고시 전부 개정 (0) | 2019.08.29 |